Die heat treatment is an important means to enhance the hardness of steel, usually after the mold is opened thick, heat treatment back and then finishing, but the process is also there is a risk, improper handling can cause cracks in steel and Scrap, then what is the reason Plastic mold steel abnormalities do:
1) There is a serious mold mesh carbide segregation.
2) There is machining or cold plastic stress in the mold.
3) Die heat treatment caused by improper operation (heating or cooling too fast, improper selection of quenching cooling medium, cooling temperature is too low, cooling time is too long, etc.).
4) Die shape complex, uneven thickness, with sharp corners and thin thread holes, so that thermal stress and tissue stress remains too large.
5) plastic mold quenching process overheating or overheating heating temperature is too high.
6) After quenching mold is not tempered or tempering Insufficient time.
7) Die repair quenching heating, without intermediate annealing again heated quenching.
8) Die heat treatment, grinding process improper.
9) Mold heat treatment after EDM, the hardened layer there is a high tensile stress and micro-cracks.
Our Recent News
- April 24, 2020
Plastic mold heat treatment problems
Related Article
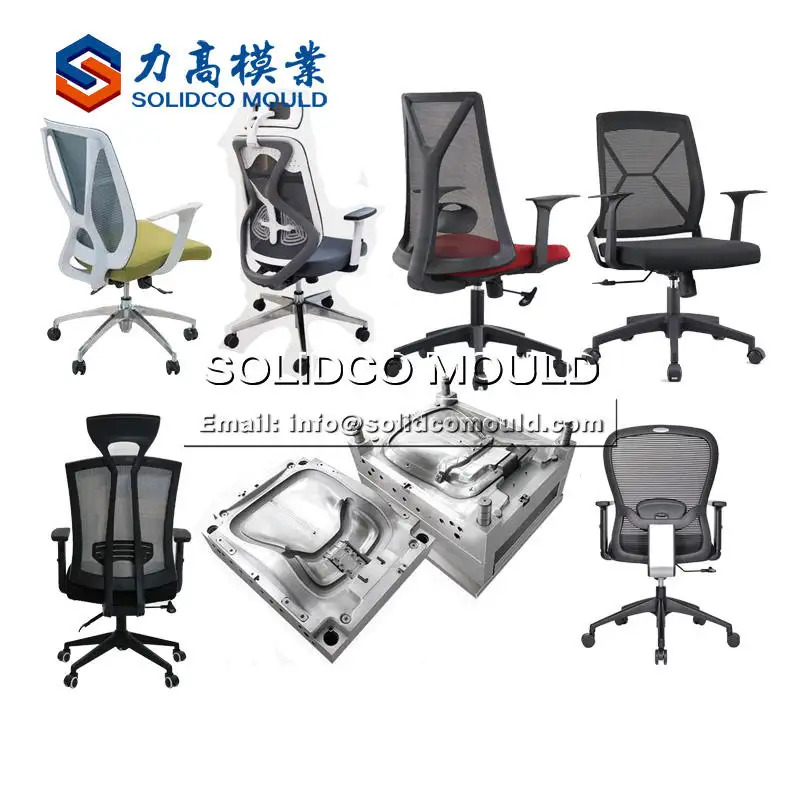
Where Precision Meets Comfort: Engineering the Future of Office Seating!
July 18, 2025
No Comments
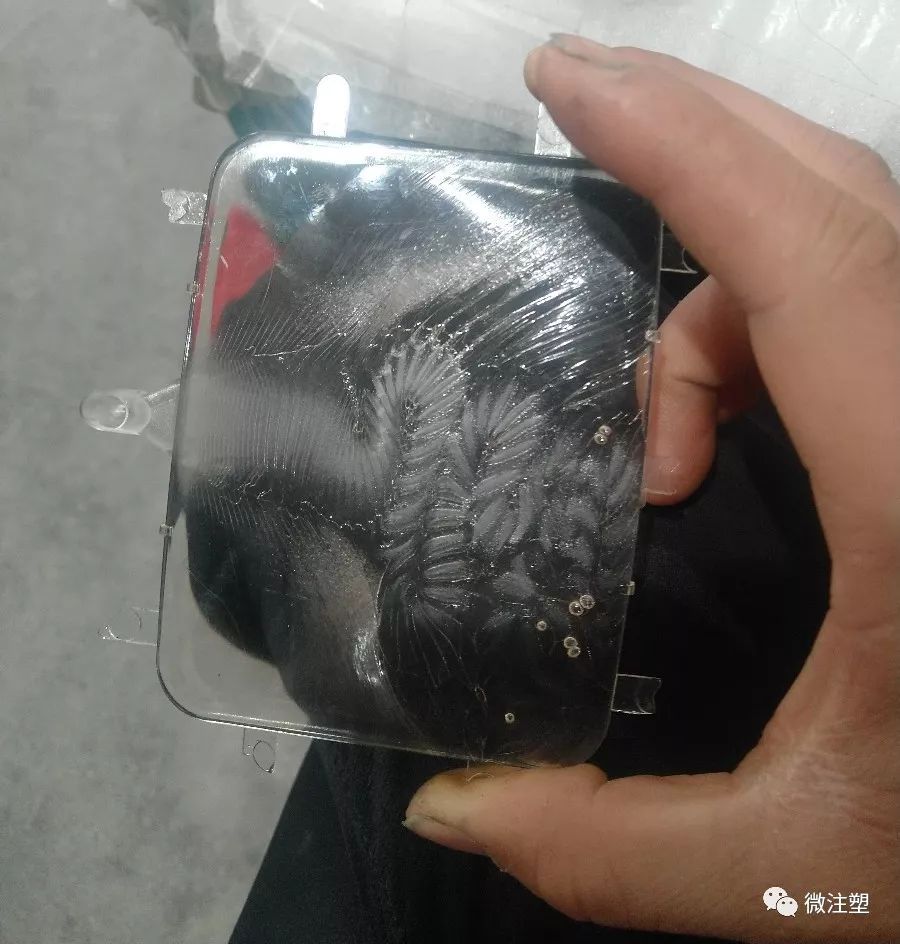
How to improve the turbidity and streaks near the gate?
July 1, 2025
No Comments
We are family in Solidco MOULD!
June 29, 2025
No Comments
Analysis And Troubleshooting Methods For Surface Gloss Of Injection Molded Parts
June 26, 2025
No Comments
Hot vs Cold Runner Systems in Molds: Key Differences Unveiled
June 24, 2025
No Comments