Moldflow Plastic Insight (MPI) is a tool that provides in-depth part and mold design analysis, which provides powerful analysis functions, visualization functions and project management tools. In-depth analysis and optimization are available for additional clients. MPI users can optimize several shapes of parts, material selection, mold design and processing parameter settings to obtain high-quality products.
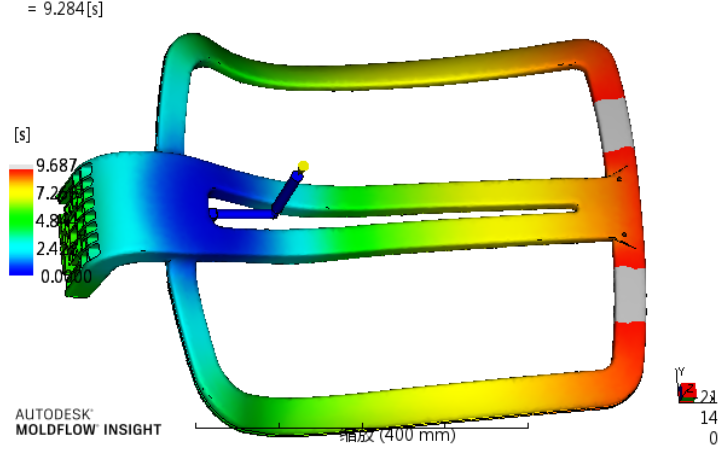
- Integrated user interface 7L integrated user interface allows users to easily input CAD models, select and search materials, establish analysis models, and conduct a series of analysis, and adopt advanced post-processing technology to enable users to observe and analyze results conveniently, It can also generate analysis reports based on Internet, which is convenient for real data sharing.
- Acquisition of CAE models MPI provides the best CAD integration solution in the CAE industry, and Moldflow realizes the most extensive integration of several models. Including wireframe models, surface modeling, thin-walled solids, and thick-walled solids that are difficult to express with medium-shaped surfaces.
Whatever the geometry of your design, MPI provides an easy-to-use, stable, and integrated environment for processing your models. For wireframe and surface modeling, MPI can directly read and analyze any CAD surface model. When users use wireframe and surface modeling files, MPI can automatically generate mid-surface meshes and accurately calculate element thickness for precise analysis. MPI’s medium surface module is used to deal with thin-walled parts, saving users a lot of CAE modeling time. Make them work on CAE analysis and optimization.
For thin-walled solids, MPI’s FUSION module is based on Moldflow’s exclusive patented DaulDomain analysis technology, enabling users to directly analyze thin-walled solid models. This reduces hours or even days of modeling work to minutes, eliminating the need for mid-surface mesh generation and modification. FUSION can read models directly from Plastic Parts Advisor for further analysis.For thick-walled solids, the MPI/Flow3D and MPI/Cool3D modules of Moldflow use a full 3D adaptive grid for full 3D analysis. These three methods provide the broadest integration of geometric design models unmatched by other software. Introduction to analysis function Simulation of injection molding flow simulation MPI flow analysis simulates the flow of plastic melt in the entire injection molding process to ensure that users can obtain high-quality parts.
Using flow analysis, users can optimize gate location and processing parameters, predict possible defects in parts, and automatically determine the size of the runner system for flow balance. Cooling simulation After the injection molding and pressure-holding processes are optimized, the cooling system modeling can be carried out: including runners, mold shapes, inserts, etc., and cooling analysis can be performed. Structural simulation MPI’s warpage analysis can predict the shrinkage and warpage of plastic parts. Both linear and non-linear methods can be used to accurately predict the amount of warpage deformation and pinpoint the main cause of warpage. MPI’s In-Mold Residual Stress Correction Algorithm (CRIMS) allows users to accurately analyze the warpage of 500 materials in the Moldflow database. The MPI stress analysis function can analyze the structural performance of the plastic part under the external force state. It provides a linear analysis method in the conceptual design stage to quickly predict whether the part meets the structural requirements of the design. A nonlinear method is used to determine the permanent deformation due to external loads. Fiber orientation analysis The fiber orientation of plastics has a significant impact on the mechanical and structural properties of injection molded parts. MPI’s advanced visualization tools enable customers to clearly see the distribution of fiber orientation in various parts of the part, thereby obtaining the stiffness information of the part . Injection Molding Parameter Optimization MPI’s injection molding process optimization function automatically determines the optimal processing parameters and injection molding machine parameters for each specific part. Its analysis results can be used as input parameters of MPX to make mold trial fast and efficient. Gas-Assisted Process Simulation Volume-controlled and pressure-controlled gas-assisted processes can be simulated using MPI. It first simulates the flow of polymer in the mold, and then simulates the penetration of gas in the cavity. Thermosetting material injection molding simulation MPI provides tools for thermosetting plastic molding simulation: such as injection molding, IC card molding, resin molding, BMC material molding and reaction injection molding, etc.