Injection molding is a method of producing shapes for industrial products. Products usually use rubber injection molding and plastic injection molding. Injection molding can also be divided into injection molding molding method and die casting method.
Introduction of injection molding process that affects the strength of injection molded parts at three points
Injection molding machine (referred to as injection machine or injection molding machine) is the main molding equipment for making thermoplastic or thermosetting materials into various shapes of plastic products using plastic molding molds. Injection molding is realized through injection molding machines and molds.
/https://solidcomould.com/product/armrest-chair-with-metal-leg-mould/
Several injection molding processes that affect the strength of injection molded parts:
1) Increasing the injection pressure can increase the tensile strength of PP injection molded parts
Compared with other hard rubber materials, PP materials are more elastic, so the density of injection molded parts will increase with the increase of pressure, which is relatively obvious. When the density of plastic parts increases, its tensile strength will naturally increase, and vice versa.
However, when the density increases to the maximum value that PP itself can achieve, the tensile strength will not continue to increase when the pressure is increased, but will increase the residual internal stress of the injection molded part and make the injection molded part brittle, so it should be enough.
Other materials have a similar situation, but the degree of obviousness will vary.
https://en.wikipedia.org/wiki/Injection_molding_machine
2) Hot oil injection molding in the mold can improve the strength of steel parts and nylon parts
Nylon and POM materials are both crystalline plastics. The mold is injected with hot oil by a hot oil machine, which can slow down the cooling speed of the injection molded parts and improve the crystallinity of the plastic. At the same time, due to the slowing down of the cooling rate, the residual internal stress of the injection molded parts is also reduced. Therefore, the impact resistance and tensile strength of nylon and POM parts injected with hot oil by hot oil machine will be improved accordingly.
It should be noted that the size of nylon and POM parts injected with hot oil by a hot oil machine will be slightly different from that of water injection molded parts, and the nylon parts may be larger.Introduction of injection molding process that affects the strength of injection molded parts at three points
- The melting speed is too fast, even if the injection molding temperature is 180°C, the rubber will be produced
Usually, pvc90 degree material is injected at 180 ℃, the temperature is enough, and generally there will be no problem of raw rubber. However, it is often due to the reason that the operator did not pay attention, or to speed up the production to speed up the melting speed, so that the screw retreats very fast. For more than one-third of the position, the time for heating and stirring the PVC material is seriously insufficient, resulting in the problem of melt temperature and uneven mixing of raw rubber, making the strength and toughness of injection molded parts quite poor.
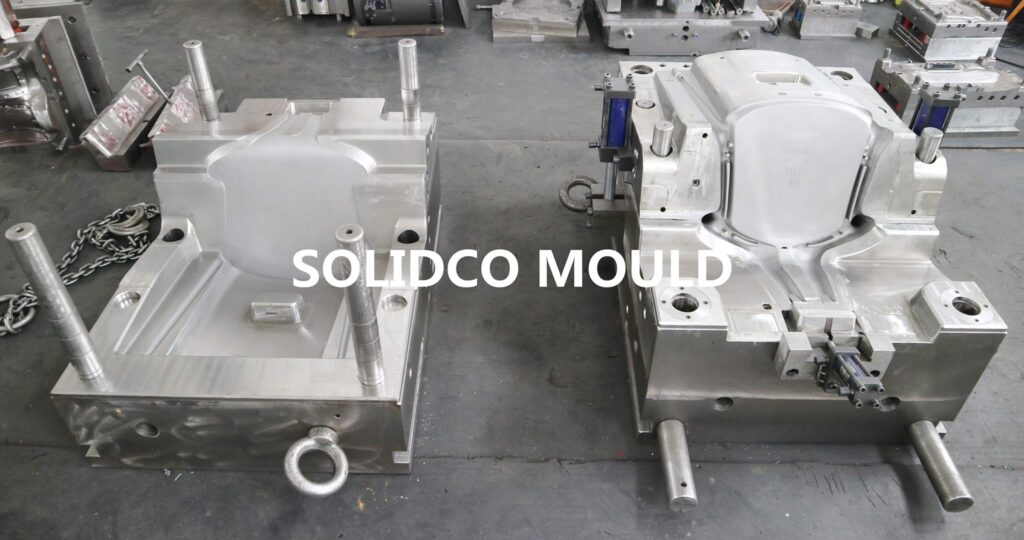
Therefore, when injecting PVC materials, be careful not to adjust the speed of the melt to more than 100 rpm. If it must be adjusted quite quickly, remember to increase the temperature of the material by 5 to 10°C, or increase the back pressure of the melt adhesive appropriately to match, and also pay attention to frequently checking whether there is any rubber problem, otherwise it is very likely to cause heavy losses.Introduction of injection molding process that affects the strength of injection molded parts at three points
Regarding this issue, because most people don’t pay much attention to it, it is specially proposed here to remind you to pay attention to it during production, and remember to do a good job in inspection.
On the contrary, it should also be noted that if the melt speed is too slow, even if it is 180-degree injection molding PVC material at 90 degrees, it will cause the problem of glue burning, especially for transparent PVC, there will be many black spots and air marks on the injection molded parts.