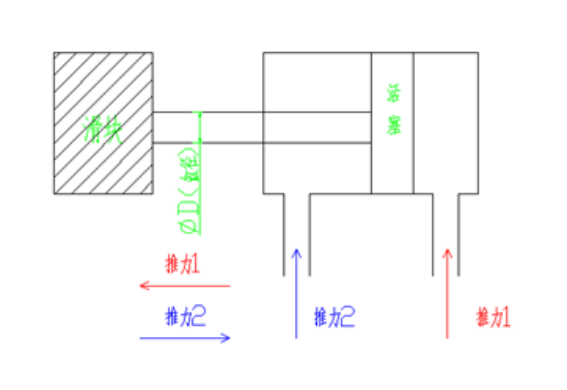
What type of oil cylinder do we use in injection molding?
Standard Cylinder
In the past, most of the oil cylinders I saw were standard oil cylinders. The first thing that comes to mind is that oil leaks from both ends every three days.
They are very heavy and require a large area to store the mold and install it in the injection molding machine. The appearance of the mold is unfair, but its advantage lies in the selection of bore and stroke.
Thin Cylinder
In recent years, thin cylinders have been used more often for molds with small strokes and compact structures. There are flat and thin appearance shapes to choose from. The advantages are that they occupy a small area, have better performance than standard cylinders, and have small mold sizes.
The cylinder is easy to repair and disassemble and has a long service life, but the price will be higher than that of a standard cylinder. Due to stroke restrictions, molds with a core pulling stroke of more than 150.00mm are rarely used.
Under what circumstances will the product use an oil cylinder?
- When the mold is using the slider to break away from the undercut, the maximum angle of the inclined guide column should not exceed 30°. If the undercut stroke exceeds 70.00mm, consider using an oil cylinder core pulling to ensure the stability of the core pulling.
- The product is reversed at the front mold, and an oil cylinder is used to simplify the mold structure and optimize mold performance.
- Use an inverted mold ejected by an oil cylinder (fixed mold ejection).
- Molds with core pulling in multiple directions require strict control of the mold opening and closing sequence.
- On molds with beveled edge core-pulling, using a slider to pull the core will result in poor stress and easy damage, while using an oil cylinder will provide smooth linear motion and change the stress situation.
- Thread molds, gear molds, molds that require an oil cylinder to drive the gear to rotate and pull the core.
- For large molds or products whose ejection stroke is larger than that of the injection molding machine, use an external oil cylinder instead of the ejection device of the injection molding machine.
How does the oil cylinder work?
Thrust 1
When the injection molding machine is set to move forward, hydraulic oil enters from the oil pipe and pushes the piston forward, causing the slider (core) to move forward.
Thrust 2
When the injection molding machine is set to move backward, hydraulic oil enters from the oil pipe and pushes the piston backward, causing the slider (core) to move backward.
What precautions should be taken when using and maintaining the oil cylinder?
- The piston of the oil cylinder is very light and thin. It is usually made of aviation aluminum and is easily damaged. When designing the oil cylinder, the mold design leaves a clearance margin of 5.00-10.00m when the piston moves forward and backward, to prevent the piston from being damaged. When we repair and use it, we must be careful not to run the cylinder dry to avoid collision damage.
- When the mold is removed from the machine and stopped for production, remember to block the oil inlet pipe of the oil cylinder to prevent the accumulated hydraulic oil from leaking and debris from falling into the oil cylinder and damaging it.
- The oil seal of the oil cylinder is a vulnerable component. When it reaches a certain number of uses, it must be replaced when the oil cylinder is removed and cleaned for maintenance of the mold.
- After the mold is installed, the pressure speed is slowly increased at the beginning, and the cylinder must be repeatedly moved to discharge the air in the cylinder before normal mold testing and debugging can be carried out.
What problems are prone to occur with the oil cylinder during injection molding?
The oil cylinder leaks and the product is oily.
- Stop the machine in time to avoid product contamination and hydraulic oil flowing into the gaps of the insert.
- Check whether the oil nozzle joint of the oil cylinder is not tightly matched/damaged.
- Disassemble the cylinder to repair the sealing device.
The cylinders advance/retreat at the same time and are not synchronized.
- Usually we move two groups of oil cylinders at the same time and connect the oil cylinders in parallel to the hydraulic valve group A/B of the injection molding machine. It may often happen that the two groups of oil cylinders are out of sync when the core advances/retreats. You can connect the parallel The oil circuit is connected in series with a set of hydraulic valves A using a tee, which can solve the problem of out-of-synchronization of the oil cylinder.
- The hydraulic valve controller, switch and circuit of the injection molding machine have poor contact.
- There are two sets of oil cylinders on the sky and earth sides. Under the action of gravity, the slider on the sky side will enter the mold first, and the one on the earth side will exit the mold first. The cylinder speed can be increased to make the neutron advance/retreat speed consistent.
The oil cylinder advances/retracts, but there is no action.
- During the production of the oil cylinder, sometimes the oil cylinder will not move. Use a heavy object to knock the mold and it will move. The sliding part may be “flattened and piled”, resulting in undercuts. It needs to be dismantled to check the sliding part. The parts are ground and re-flyed.
- The hydraulic oil of the injection molding machine is dirty/deteriorated, and the hydraulic valve is clogged or damaged.
- The product is too full, and the wrapping force of the oil cylinder is too great, making it impossible to twitch.
- The hydraulic valve controller, switch and circuit of the injection molding machine have poor contact.
When the oil cylinder is on the sky side, slide it down after opening the mold.
There may be oil leakage in the oil cylinder, or there may be oil leakage in the hydraulic system of the injection molding machine. Check the hidden dangers in time to prevent mold compression. For molds or equipment where the cylinder often slides down, adding a circlip or spring to the bottom of the slider can prevent the mold from happening.
The slider runs to remove the edges/burrs.
- When designing the mold, try to avoid spot sealing on the parting surface, and at least a 5.0mm penetration surface should be left at the glue position.
- Both sides of the sliding part of the oil cylinder need to be inserted and matched at 2-5° to avoid straight-face insertion without angle.
- For slides exceeding 100.00mm, a shovel should be designed, and an extra 5.00-10.00mm of wear-resistant block should be left to prevent the shovel from being unable to press the slider and causing the slider to move backward when filling products.
- Regularly maintain the mold to prevent excessive material chips from falling into the sliding part of the cylinder during long-term operation, which will affect the twitching of the cylinder.
Improper operation, molding
- For molds that require the sequence of opening and closing the mold, install a limit switch. The injection molding machine uses “position” to connect to the injection molding machine and control the opening and closing mold detection system.
- For molds with oil cylinders on the sky side, a limit switch should be installed to prevent the oil cylinder from sliding down.
- The mold that “pulls the core first and then opens the mold”/”pulls the core first and then ejects” should be equipped with a limit switch. Non-technical personnel are prohibited from operating the machine, and a mold opening and closing sequence diagram should be configured.
Contact Person: Alex Chu
WhatsApp/ WeChat: 0086 18968677763
Email: sc10@solidcomould.com
Website: www.solidcomould.com