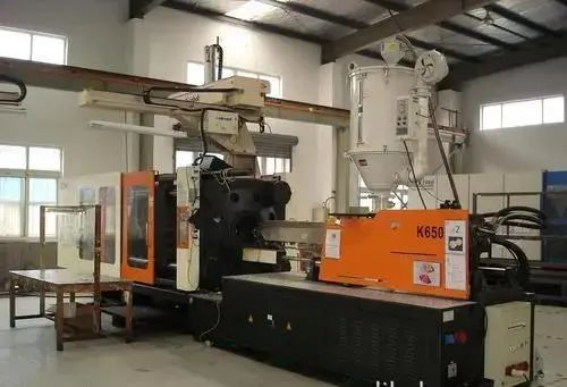
The proportion of plastic materials in our daily life is getting higher and higher, and the requirements for their quality are also getting higher and higher.
As an important production method, injection molding is becoming more and more urgent to improve technology, and the influencing factors of injection molding products. There are many, and the impact of each process parameter on product performance is introduced below.
Injection molding conditions and effects
During the molding process, precision molding machinery, reasonable mold design, and excellent material properties can only be reflected with reasonable molding process settings.
On the other hand, defects in molding machinery, mold design, and material properties can sometimes be resolved through appropriate molding processes. settings to compensate
Injection molding process conditions have an impact on the appearance and mechanical properties of plastic products. Each process condition parameter affects each other and is not independent. Some product defects are the result of mutual influence.
Injection pressure
Injection pressure refers to the pressure exerted by the top of the screw or the plunger on the plastic melt during the injection process. Its function is to mix and plasticize the melt.
The screw (or plunger) must provide the ability to overcome the flow resistance of solid particles and melt in the barrel and nozzle. The plastic melt fills the mold cavity at a certain speed, and the injection pressure plays a compacting role after the mold cavity is filled with melt.
This makes the plastic part dense and compensates for the shrinkage of the molten material due to cooling, so that the plastic part maintains a precise shape and obtains the required performance.
The injection pressure is mainly determined by the type of plastic, the type of injection molding machine, the temperature of the mold, the mold structure, and the wall thickness of the plastic part. The size and structure of the gating system have a great influence on the injection pressure.
Holding pressure
When the melt fills the cavity, the injection pressure plays the role of compacting the melt in the mold. At this time, we also call the injection pressure the holding pressure. In actual production, the holding pressure should be equal to or less than the injection pressure. pressure used.
When the pressure during holding is equal to the pressure during injection, the shrinkage rate of the plastic part will often be reduced, and the stability of the plastic part and the mechanical properties of the plastic part can be ensured.
But it is often accompanied by an increase in residual stress during demoulding, making it difficult to demould plastic parts, making plastic parts prone to deformation, surface scratches, etc.
It is also easy to cause flash edges in plastic parts, affecting the apparent quality. Therefore, when selecting the holding pressure, many aspects need to be considered and the choice must be made carefully.
Generally speaking, the impact of holding pressure on product quality is similar to that of injection pressure. The holding pressure of most plastics is between one and one of the injection pressure.
The determination of the specific holding pressure mainly considers the characteristics of the plastic part material and the structure of the part, and overcomes the flow resistance of the melt from the barrel to the mold cavity. Feed the molten material into the mold cavity and compact it.
Plasticizing pressure
Plasticizing pressure refers to the pressure on the melt at the top of the screw when the screw retreats. Its impact on injection molding is mainly reflected in the plasticizing effect of the injection machine on materials and its plasticizing ability.
Generally speaking, as the plasticizing pressure increases, the screw retreat speed decreases, and the pressure on the melt in the barrel increases. Therefore, the shearing effect during plasticization is strengthened and the plasticizing effect is improved.
However, it should be noted that while increasing the back pressure, the excessive plasticizing pressure reduces the plasticizing amount due to the backflow and leakage of the melt at the edge of the screw channel, which may cause insufficient metering.
The shear heat will be too high and the shear stress will be too high, which may degrade the material, produce bubbles or burns, and affect the quality of the plastic parts.
Mold temperature
Mold temperature refers to the temperature of the mold cavity surface during the molding process. Mold temperature affects the filling flow behavior of the melt, the cooling rate of the product, and the performance of the product after molding.
The setting of mold temperature mainly depends on the viscosity of the melt. If the melt viscosity is low, low mold temperature injection can be used to shorten the cooling time and improve production efficiency. If the melt viscosity is high, high mold temperature injection molding should be used.
Generally speaking, increasing the mold temperature can make the cooling rate of the part uniform and prevent the occurrence of molding defects such as dents and cracks. The mold temperature control of crystalline plastics directly determines the cooling rate, which further determines the crystallization rate.
When the mold temperature is high, the cooling rate is small and the crystallization rate becomes large, which is conducive to the relaxation process of molecules and the molecular orientation effect is small. If the mold temperature is too high, it will prolong the molding cycle and make the product brittle.
The mold temperature is low, the cooling rate is large, and the flow of the molten material and crystallization proceed simultaneously. Since the residence time of the molten material in the crystallization temperature + range is shortened, it is not conducive to the growth of the crystal, resulting in a low degree of molecular crystallization of the product, affecting its performance.
In addition, if the mold temperature is too low, the flow resistance of the plastic melt is very large, the flow rate slows down, and it may even solidify during the mold filling, hindering subsequent feeding, resulting in short shots of the parts and large forced orientation, often resulting in plastic parts lacking material, dents, and Defects such as weld seams.
Barrel temperature
In order to ensure the normal flow of the plastic melt without causing it to deteriorate or decompose, the barrel temperature needs to be appropriately selected. Plastics with large average molecular weight and concentrated molecular weight distribution, as well as glass-reinforced plastics, should choose materials with higher temperatures. barrel temperature.
The temperature of the barrel is generally arranged according to the principle of high in the front and low in the rear. However, when the plastic contains too much water, the rear end temperature can also be appropriately increased.
Nozzle temperature
In order to avoid the melt casting phenomenon at the nozzle, it is usually necessary to make the nozzle temperature slightly lower than the maximum temperature of the barrel. In the case of low-speed air injection, the ejected melt flow without bubbles and smooth is generally regarded as Temperature appropriate standards.
Melt temperature
The melt temperature mainly depends on the temperature of the barrel and the nozzle, which affects the plasticization of the material and the injection molding of the melt. The increase in injection temperature is mainly beneficial to improving the fluidity of the melt, which is related to many characteristics of the product.
Increasing the melt temperature can reduce the internal stress of the plastic part, impact strength and deflection in the streamline direction, tensile strength and other mechanical properties, while reducing the impact strength, flow length and surface roughness perpendicular to the streamline direction. The properties are improved and the post-shrinkage of the product can be reduced.
Generally speaking, increasing the melt temperature is beneficial to improving the filling condition and transfer within the mold cavity, reducing orientation, etc., and is beneficial to improving the overall performance of the product, but too high a temperature is not advisable.
When the melt temperature is close to the upper limit of the injection molding temperature range, on the one hand, it is easy to produce more gas, causing bubbles, holes, discoloration, scorching, etc. in the plastic parts. It also produces flash due to excessive improvement in fluidity.
Affecting the apparent quality of the product On the other hand, excessive temperature will degrade the plastic, reduce the strength of the plastic part, lose elasticity, etc., affecting the performance.
Injection time
Injection time is one of the parameters that controls the injection rate. The shorter the injection time, the higher the injection rate. The injection rate has a great impact on the performance of the plastic parts.
Increasing the injection rate can increase the filling pressure, which is beneficial to the mold filling process and reduces heat loss during mold filling. The temperature of the mold cavity is relatively uniform, and the product is uniform and dense. At the same time, it can reduce the shrinkage rate of the product, reduce the core orientation of the plastic part, and increase the strength of the weld seam.
Increasing the injection rate is beneficial to the overall performance of the product, but an excessively high injection rate will increase pressure loss, reduce the thickness of the solidified layer, improve the surface orientation of the plastic part, and even cause elastic turbulence in the melt, making the plastic part prone to flash edges and Surface cracks, etc.
Experiments have proven that either too high or too low an injection rate will lead to a decrease in impact strength. On the other hand, too low an injection rate will reduce the strength of the weld seam of the plastic part, increase the total orientation effect, increase the internal stress, etc., affecting the mechanical properties of the product.
Compress time
The length of pressure holding time and cooling time also have a direct impact on the quality of plastic parts. Shortening the holding time will accelerate the decrease in mold cavity pressure, which may cause backflow, cause defects such as shrinkage holes and dents in the plastic parts, and affect the dimensional stability of the plastic parts.
Lengthening the holding time can improve the dimensional stability of the plastic parts, avoid the occurrence of the above defects, and obtain dense products. At the same time, the mold cavity pressure will increase and the internal stress caused by temperature unevenness will be changed. However, it will increase the difficulty of demoulding, and sometimes it is easy to scratch the surface or bend the plastic part.
The length of material plasticization time can affect the plasticization quality and directly affect product performance. If the time is too short, the plasticization will not be uniform and the temperature will be consistent, and hard lumps, silver wires, etc. will easily occur. If the time is too long, the melt will decompose and burn due to the action of the screw, which will also have a negative impact on product quality.
Special process impact
Vibration injection molding, under high vibration pressure, as the vibration frequency increases, the tensile properties and notch impact strength of the product are significantly improved. In addition, the addition of ultrasonic technology can also have good results.
Contact Person: Alex Chu
WhatsApp/ WeChat: 0086 18968677763
Email: sc10@solidcomould.com
Website: www.solidcomould.com