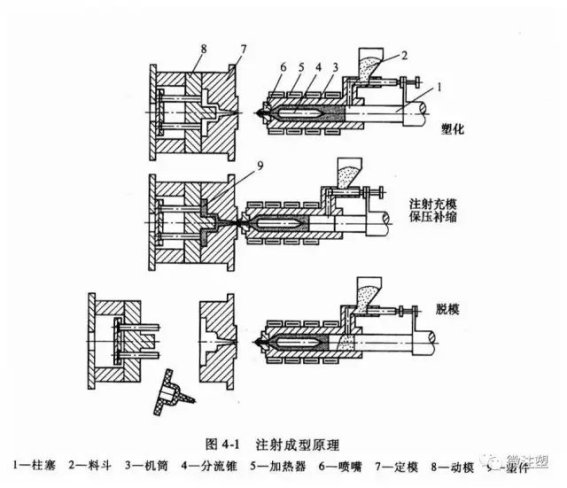
Injection molding principle
Taking the plunger injection machine as an example, the granular or powdery plastic is first fed from the hopper of the injection machine into the barrel equipped with a heating device for heating, melting and plasticization to turn it into a viscous flow melt, and then in the column of the injection machine.
Driven by the high pressure of the plug, it is injected into the closed mold cavity with a lower temperature through the nozzle at the front end of the barrel at a very high flow rate.
After a period of pressure-maintaining cooling and shaping, the mold is opened and parted, and the mold can be separated from the mold cavity (molded plastic parts). Plastic parts (plastic parts) with a certain shape and size are taken out of the closed space), thus completing a molding cycle.
Characteristics and applications of injection molding
Injection molding has the advantages of strong adaptability to plastic varieties, and can mold plastic parts with complex shapes, precise dimensions, and metal or non-metal inserts in one go.
It has high production efficiency and is easy to realize automation. It is an important method for thermoplastic plastic molding. method.
The injection molding process is developing rapidly. In addition to thermoplastic injection molding, some thermosetting plastics can also be successfully used for injection molding, and have the characteristics of high efficiency and stable product quality;
low anti-foaming plastics (density is 0.2-0.9g/cm3 ) injection molding can produce plastic parts with excellent properties such as buffering, sound insulation, and heat insulation; two-color or multi-color injection molding can produce plastic products in various colors, beautiful appearance, and application.
In addition, the application of hot runner injection molding technology has obvious advantages in obtaining large plastic parts and reducing or eliminating condensation in the gating system. Injection molding is also an important process for obtaining parisons for hollow plastic products.
Injection machines and injection molding systems
The injection machine is the key equipment for injection molding production. The injection molding system refers to the injection system, mold clamping system and the mold installed on the injection machine that are directly used for the molding action.
Classification according to appearance and structural characteristics
Horizontal injection machine
The horizontal injection machine is the most basic and common form of injection machine products. Its structural feature is that the injection system of the molding material coincides with the axis of the mold clamping mechanism and is parallel to the ground.
The advantage is that the body is low and stable. It is more convenient to add materials, operate and maintain, and the product can automatically fall after being pushed out of the mold, making it easy to implement mechanization or automation.
However, it has disadvantages such as inconvenient disassembly and assembly of the mold, troublesome installation of inserts, and large floor space.
Vertical injection machine
The structural feature of this injection machine is that the axes of the injection system and the mold clamping mechanism are coincident and vertical to the ground.
This structure has the advantages of small floor space, easy disassembly and assembly of the mold, easy installation of inserts, and the materials in the hopper can evenly enter the barrel.
However, after the product is released from the mold, it needs to be taken out manually, and it is not easy to achieve mechanization or automation.
Right angle injection machine
The structural feature of this injection machine is that the axes of the mold clamping mechanism and the injection system are perpendicular to each other. The use and installation characteristics are between the previous two types of injection machines. It is especially suitable for producing asymmetrically shaped plastic parts and molds using side gates.
At present, the most commonly used right-angle injection machines in China clamp the mold in the horizontal direction and inject in the vertical direction. The mold closing mechanism adopts screw drive and is widely used. Right-angle injection machines that clamp the mold in the vertical direction are less commonly used.
Injection machine specifications and main technical parameters
At present, the specifications of injection machines are usually characterized by the injection volume (ie, injection capacity) and the size of the clamping force.
The theoretical volume of plastic that can be injected by the plunger or screw in the barrel of the injection machine in one injection stroke is called the injection volume, which is the main parameter characterizing the capability of the injection machine.
According to international standards, the nominal injection volume in the specifications of the injection molding machine needs to be expressed as a numerical value under constant pressure conditions (injection pressure is 100MPa).
During the working process of the injection machine, the force that locks and closes the mold cavity to prevent the melt from overflowing is called the clamping force. The size of the clamping force is related to the molding area allowed by the injection machine.
Mold clamping system of injection molding machine
The function of the mold clamping system is to realize the opening and closing action of the mold, to lock the mold during injection, and to push out the plastic parts in the mold when opening the mold.
The most basic requirement for the mold clamping system of injection molding is to provide a reliable clamping force for the mold during mold clamping, so as to prevent the mold from expanding along the parting surface under the pressure of the plastic melt, causing edge separation in the product and affecting accuracy.
Contact Person: Alex Chu
WhatsApp/ WeChat: 0086 18968677763
Email: sc10@solidcomould.com
Website: www.solidcomould.com