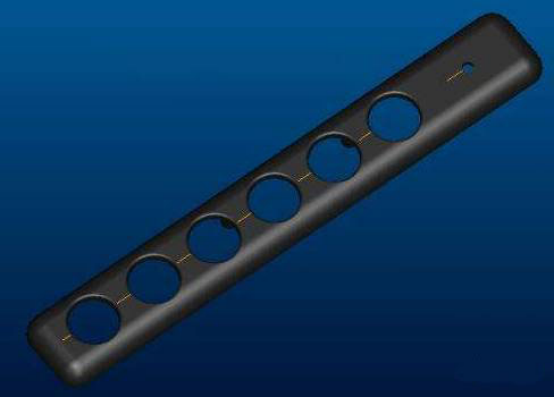
Weld mark formation mechanism
Weld marks (also called water lines) are intersection marks formed when molten plastic flowing out of gates at different locations in the mold converges. The reason for the formation of weld marks is that the temperature, pressure, and speed of the molten material flowing out of each gate are not completely consistent when it reaches the convergence point through the complex-shaped cavity.
The seams formed when the melts merge are divided into meld lines and weld lines. The performance of the meld line is significantly better than that of the weld line. Generally speaking, a fusion line is formed when the convergence angle is greater than 135 degrees, and a weld mark is formed when it is less than 135 degrees.
The performance of the fusion line is obviously better than that of the weld mark. The convergence angle has an important influence on the performance of the weld seam because it affects the full degree of fusion, entanglement and diffusion of the molecular chains after welding. The larger the convergence angle, the better the performance of the weld seam.
Causes of weld marks
- The plastic melt that passes through the gate at high speed directly enters the mold cavity, then contacts the surface of the mold cavity to solidify, and is then pushed by the subsequent plastic melt, leaving traces of snaking.
- When the mold adopts a multi-gate pouring scheme, the plastic melt flow fronts merge with each other; the melt flow fronts will also be divided into two in the hole and obstacle areas; uneven wall thickness will also cause weld marks .
- Use side gates. If there is no stagnant area after the plastic passes through the gate or the stagnant area is insufficient, it is easy to produce spray marks.
Solutions to weld marks
Plastic has poor fluidity
Improve the stagnation phenomenon of the mold pouring system, expand the gate, runner and injection port, and improve the fluidity of the material
Adding too much reinforcing material
The higher the glass fiber content, the lower the weld line strength. When the aspect ratio of glass fiber increases, the strength of the weld line decreases.
The wall thickness of the product is too thin or the wall thickness difference is too large
Optimize product wall thickness.
Wavefront convergence angle is too small
When the wavefront convergence angle is less than 135°, a fusion line is formed; when it is greater than 135°, a fusion line is formed. Compared with the fusion line, the molecules on both sides of the weld line diffuse less each other and are of poorer quality.
When the meeting angle is between 120° and 150°, the surface traces of the welding line gradually disappear. The increase in the intersection angle can be achieved by adjusting the thickness of the product, changing the position and number of gates, changing the position and size of the runner, etc.
Mold temperature is too low
Increase the mold temperature and reduce the coolant flow in the mold
The runners and gates are not in the right position or are too small or too long
The length of the gate is generally less than 1mm. Anything longer than this can easily cause problems. The use of gate inserts makes it easier to modify the gate size.
Start testing gates from a small size, with an increment of 10% as a rule. For example, if 0.50mm is too small, try 0.55mm next time. Adjust the gate position so that the weld mark moves to an invisible position.
Poor mold exhaust
Check whether there is a cold material cavity or whether its position is correct, and add an exhaust groove or exhaust hole in the under-injection area. For crystalline materials, the exhaust groove gap is: 0.025mm; for amorphous materials, the exhaust groove gap is: 0.035mm.
Injection speed is too low
Increase injection speed
Holding pressure too low
Increase holding pressure and switch to holding pressure as early as possible
Material temperature is too low
Properly increase the temperature of the barrel and nozzle, extend the injection cycle, and reduce the coolant flux in the mold
Insufficient flow of molten plastic
Increase injection flow or gate size
Injection molding machine material tube temperature is too low
When the temperature of the material tube is too low, when the melt wave front forms a weld line, the temperature is too low, the joint is poor, and the lines are obvious. Increase the material temperature so that when the melt wave front forms a weld line, the temperature is moderate and the line is not obvious.
When the weld line is formed, the difference in temperature between the two wave fronts and the temperature of each wave front, as well as the pressure after the weld line is formed, determine the quality of the weld line. The lower the temperature, the greater the temperature difference (above 10°C), the smaller the pressure, the worse the quality.
Insufficient back pressure
Increasing back pressure can improve weld line quality.
Injection pressure or rate of fire is too low
Increasing the injection pressure or rate of fire can naturally improve it. Injection pressure and rate of fire are related, and it is not appropriate to increase both at the same time. Because before the adjustment, it was not clear whether the cause of the obvious weld line was the injection pressure or the rate of fire.
You should choose one adjustment, observe its effects, and then decide on the next step. The increment of each injection pressure or firing rate adjustment is based on 10%. After each adjustment, it takes about 10 injections to reach a stable state.
Contact Person: Alex Chu
WhatsApp/ WeChat: 0086 18968677763
Email: sc10@solidcomould.com
Website: www.solidcomould.com