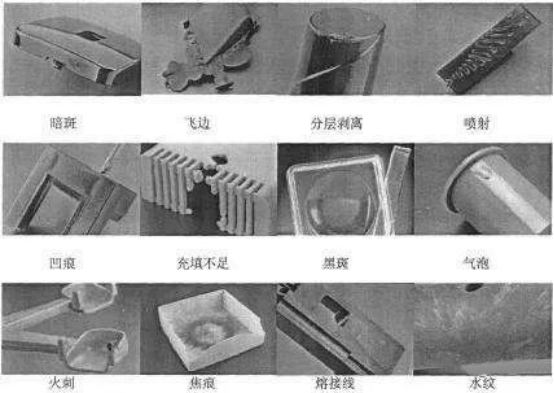
Not enough (lack of glue)
Process problems: plasticizing temperature is too low, nozzle temperature is too low, injection time is too short, injection speed is too slow, mold temperature is too low.
Mold problems: the runner is too small, the gate is too small, the gate position is unreasonable, the exhaust is poor, and there are debris in the cavity.
Raw material problems: poor fluidity and mixed with impurities.
Flash
Process problems: The plasticizing temperature is too high, the injection time is too long, the amount of material added is too much, the injection pressure is too high, the mold temperature is too high, and there are debris between the templates.
Mold problems: mold deformation, matching size errors between the core and cavity, template combination not parallel, exhaust groove too deep.
Equipment problems: the templates are not parallel and the templates are not closed tightly.
Raw material problem: excessive liquidity.
Deformation
In terms of process conditions: material temperature is too high, mold temperature is too high, pressure holding time is too short, cooling time is too short and forced demoulding.
In terms of molds: Improper gate position, insufficient number of gates, improper ejection position causes uneven stress.
Flow marks
In terms of process conditions: the material temperature is too low and is not fully plasticized, the injection speed is too low, the injection pressure is too small, the holding pressure is not enough, the mold temperature is too low, and the injection volume is insufficient.
In terms of molds: the gate is too small, the number of gates is too few, the runner gate is rough, and the surface finish is poor.
In terms of equipment: the system failed after temperature control and the oil pump pressure dropped.
In terms of raw materials: Containing too many volatiles, poor fluidity, and mixed with impurities.
Bubble
In terms of process conditions: low injection pressure, insufficient holding pressure, insufficient holding time, and too high material temperature;
Mold aspects: poor exhaust, unreasonable gate location, gate size too small;
In terms of raw materials: the moisture content is not dried or the drying time is not enough, and the shrinkage rate is too large.
Shrinkage
In terms of process conditions: insufficient feeding amount, too short injection molding time, too short holding pressure time, too high material temperature, too high mold temperature, and too short cooling time;
In terms of molds: the runner is too small, the gate is too small, and the exhaust is poor;
In terms of equipment: the injection pressure is not enough and the nozzle is blocked by foreign matter;
In terms of raw materials: the shrinkage rate is too large.
Dimensional instability
In terms of process conditions: the injection pressure is too low, the barrel temperature is too high, the holding pressure time changes, the injection cycle is unstable, and the mold temperature is too high;
In terms of molds: uneven gate size, inaccurate cavity size, loose core, too high mold temperature or no water channel;
In terms of raw materials: there are changes in brand varieties, uneven particle sizes, and volatile substances.
Difficulty in demolding
In terms of process conditions: the injection pressure is too high, the holding time is too long, the injection volume is too much, and the mold temperature is too high;
Equipment: Insufficient ejection force and insufficient ejection distance;
Mold aspects: no demoulding slope, insufficient smoothness, improper ejection method, improper matching accuracy, poor exhaust, and template deformation.
Silver streak
In terms of process conditions: material temperature is too high, injection speed is too fast, injection pressure is too high, plasticization is uneven, and too much release agent;
In terms of molds: the gate is too small, the mold finish is poor, and the exhaust is poor;
In terms of equipment: the back pressure is too low and there is cast material on the nozzle;
In terms of raw materials: containing moisture but not drying, excessive lubricant
Burnt
In terms of process conditions: the material temperature is too high, the injection pressure is too high, the speed is too fast, the downtime is too long, and the release agent is not clean;
In terms of molds: the gate is too small, poor exhaust, complex cavity, and poor cavity finish;
In terms of raw materials: there are impurities mixed in the materials, and there are powder materials in the granular materials.
Discoloration
In terms of process conditions: the material temperature is too high, the injection pressure is too high, the molding cycle is long, the mold is not cooled, and the nozzle temperature is high;
In terms of mold: the gate is too small;
Equipment: There are obstacles in the barrel or nozzle, and the screw speed is high. The core and the center of the nozzle are not concentric;
In terms of raw materials: material contamination, decomposition of colorants, and high volatile content.
Weld Line
In terms of process conditions: low injection pressure, short injection time, low material temperature, too large clamping force, and inappropriate release agent;
In terms of mold: the mold temperature is too low, the flow channel is small, the gate position is wrong, and the exhaust is poor;
Equipment: poor plasticization;
In terms of raw materials: the fluidity is too poor, there is too much lubricant, and there are foreign matter in the material.
Gloss defects
In terms of process conditions: the material temperature or mold temperature is low, the injection pressure is too low, the injection speed is too large or too small, and the cooling time is too short;
In terms of molds: the roughness of the mold becomes larger, the gate is too small, the flow channel is too thin, and the exhaust is poor;
Equipment: Insufficient supply of materials;
In terms of raw materials: the raw materials are not dried or contain volatile substances, the raw materials are easy to degrade, the additives or release agents are used in excessive amounts or are of poor quality, and contain foreign matter.
Contact Person: Alex Chu
WhatsApp/ WeChat: 0086 18968677763
Email: sc10@solidcomould.com
Website: www.solidcomould.com