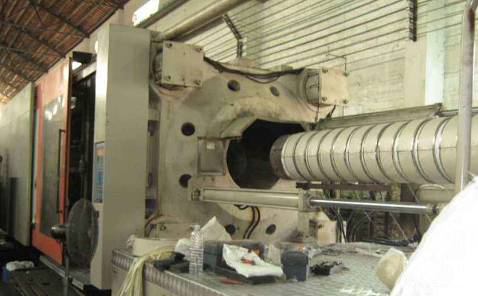
Pre-molding action selection
Depending on whether the injection seat retreats before and after pre-plastic feeding, that is, whether the nozzle leaves the mold, the injection molding machine generally has three options:
Fixed feeding: the nozzle is always attached to the mold before and after pre-molding, and the injection seat does not move.
Front feeding: The nozzle is pressed against the mold for pre-molding and feeding. After pre-molding is completed, the injection seat retreats and the nozzle leaves the mold.
The purpose of choosing this method is to use the injection hole of the mold to press against the nozzle during pre-molding to prevent the melt from flowing out of the nozzle when the back pressure is high. After pre-molding, it can avoid the heat transfer caused by long-term contact between the nozzle and the mold, affecting their respective The temperature is relatively stable.
Post-feeding: After the injection is completed, the injection seat retreats, the nozzle leaves the mold and then is pre-molded. After pre-molding is completed, the injection seat advances. This action is suitable for processing plastics with a particularly narrow molding temperature. Due to the short contact time between the nozzle and the mold, heat loss is avoided and the solidification of the molten material in the nozzle hole is avoided.
After the injection is completed and the cooling timer is completed, the pre-molding action begins. The screw rotates to melt the plastic and squeeze it to the front of the screw head. Because the check ring at the front end of the screw acts as a one-way valve, molten plastic accumulates at the front end of the barrel, forcing the screw backward.
When the screw retreats to a predetermined position (this position is determined by the travel switch, which controls the retreat distance of the screw to achieve quantitative feeding), the pre-molding stops and the screw stops rotating.
This is followed by a retraction action, which means that the screw makes a slight axial retreat. This action can relieve the pressure of the melt accumulated at the nozzle and overcome the “salivation” caused by the imbalance of pressure inside and outside the barrel. Phenomenon.
If retraction is not required, the retraction stop switch should be adjusted to the appropriate position so that at the same time that the pre-molding stop switch is pressed, the retraction stop switch is also pressed. When the screw retracts and the stop switch is pressed, the retraction stops.
Then the Sagittarius began to retreat. When the shooting base retreats until the stop switch is pressed, the shooting base stops retreating. If a fixed feeding method is used, attention should be paid to adjusting the position of the travel switch.
Generally, fixed feeding methods are used in production to save the time of advancing and retracting the injection seat and speed up the production cycle.
Screw back pressure and speed control
High back pressure can cause strong shearing of the melt, and low rotation speed can also cause the plastic to be plasticized in the barrel for a long time. Therefore, the simultaneous programming control of back pressure and rotational speed is often used.
For example: during the entire screw metering stroke, first use high speed and low back pressure, then switch to lower speed and higher back pressure, then switch to high back pressure and low speed, and finally plasticize at low back pressure and low speed.
In this way, the pressure of the melt at the front of the screw is mostly released, reducing the rotational inertia of the screw, thereby improving the accuracy of screw metering.
Excessive back pressure often causes:
- The degree of discoloration of the colorant increases;
- The mechanical wear of the barrel screw of the pre-molding machine increases;
- The pre-molding cycle is extended and production efficiency decreases;
- The nozzle is prone to salivation and the amount of recycled material increases;
Even if a self-locking nozzle is used, fatigue damage will occur if the back pressure is higher than the designed spring locking pressure. Therefore, the back pressure must be adjusted appropriately.
Contact Person: Alex Chu
WhatsApp/ WeChat: 0086 18968677763
Email: sc10@solidcomould.com
Website: www.solidcomould.com