The most commonly used chamfers are divided into
Round
and
chamfer
Rounding refers to connecting two curved surfaces of a part tangently through a rounded surface. A standard rounded corner usually uses a radius value R to represent its size. Structural design of plastic parts: chamfering
Chamfering refers to connecting two curved surfaces of a part at an angle through a beveled surface. The standard bevel angle usually uses a distance value C to express its size. The standard angle value is 45°. 02 The difference between rounded corners and beveled corners
Both fillets and bevels can be used to blunt sharp edges or create a gradual transition between two meeting surfaces. From this point of view, they are universal, however, there are differences between fillets and chamfers in many applications.https://solidcomould.com/product-category/injection-mould/pipe-fitting-mould/
- Processing method
For ordinary machining, both internal and external fillets in the vertical direction can be processed easily, but internal bevels cannot be processed. Fillets require a specific size tool to machine fillets of various radii (a larger fillet radius than the cutter is is good practice during machining.), bevels do not require a specific size tool, and different sizes of chamfers must be made. For corners, you only need to control the amount of cutting. It should be noted that for CNC machining, the processing time of fillets and chamfers is the same.
- Function
Both fillets and bevels can reduce stress concentration and optimize flow, but fillets are a continuous transition, while bevels are linear transitions. There are still edges after beveling. Compared with chamfers, fillets provide Lower stress concentration and smaller flow resistance. For this reason, rounding is better than chamfering on plastic parts, unless rounding is continued on both edges of the bevel.
However, if your design is for screw holes, positioning holes, and positioning posts, using fillets is not a good choice. The smaller, sharper edge of the beveled end will help it move down the hole more smoothly as opposed to a rounded corner, making assembly easier.
Furthermore, chamfering can also make tapered counterbore holes, while rounding does not have this function. 3. Aesthetics
From an aesthetic perspective, rounded corners are often prioritized in industrial design due to their visually pleasing properties. The properties of rounded corners are soft and comfortable, giving people a sense of security and intimacy. The bevel gives people a sharp and aggressive feeling. Generally, bevels are rarely used in large areas in consumer products, but bevels can create a unique appearance in certain details and provide the finishing touch.
Depending on your design requirements, you can use both fillets and chamfers on the outer edges. If appearance is not important to your design, such as a metal machined part, you can opt for a simple bevel to blunt the sharp edges, which will help reduce the cost of the part.
On the other hand, if your design needs to look beautiful and you have to use rounded corners, you must pay attention to the size of the inner corner radius. If the radius is too small, it may not be possible to use the tool to directly process it in place, and you have to use more expensive and longer processing methods such as EDM or wire cutting. The larger the radius, the easier it is to process (the larger the radius, the larger the radius can be used). The shorter the processing time, the deeper the processing depth).
03 Factors to consider when choosing between fillets and chamfers
Structural engineers often find themselves in uncertainty when choosing fillets or chamfers for their designs. To avoid getting into this mess, here are a few things you should consider.https://doi.org/10.1016/j.jmrt.2023.08.241
- For machine-added parts
- Processing time and cost
If you simply want to blunt sharp corners to prevent scratches, chamfering is a better choice because chamfering requires less time and is more cost-effective. However, if you are using CNC machining instead of regular milling, there is no significant time difference between them, the only time difference will be the time required to change the tool.
Bottom edges (concave fillets) like these are particularly challenging to make with CNC machines because they require specialized tooling such as ball end mills, which are fragile and cut at slower cutting speeds. Cutting will increase the manufacturing cost. Therefore, it is best to cancel the rounded corners on the bottom edge. If rounded corners are necessary, consider making the rounded corners as large as possible.
- Coating coverage
Rounded corners are easier to coat than beveled corners. This is because fillets slowly transition and connect tangentially to adjacent faces, resulting in a thicker, more uniform coating adhering to the part compared to a beveled edge.
- Stress concentration
If the design goal is to reduce stress concentrations, fillets are a better choice because fillets of the same size have a greater surface area to share stress than bevels.
- Hole or pin
Whether it is a screw hole, a locating hole, or a locating pin, chamfering the edge of the hole or pin is a better choice.
- For plastic parts
Since the molding method of plastic parts is different from that of machined parts, the chamfering design of plastic parts is mainly based on rounded corners, supplemented by bevels (bevels are more for modeling needs and some structures play a guiding role. There is also a gradient transition of wall thickness), and the design of rounded corners has the following benefits:
- Liquidity
During the injection molding process of plastic parts, the fluidity of the molten resin is very important. The rounded corners provide smaller flow resistance. The larger the rounded corners, the easier it is for filling.
In the original design, sharp corners can easily cause air entrapment due to eddy currents during the injection molding process, resulting in local high temperatures that burn the sharp corners of the part, causing appearance defects. After optimization, the radius is increased to ensure the flow of plastic melt.
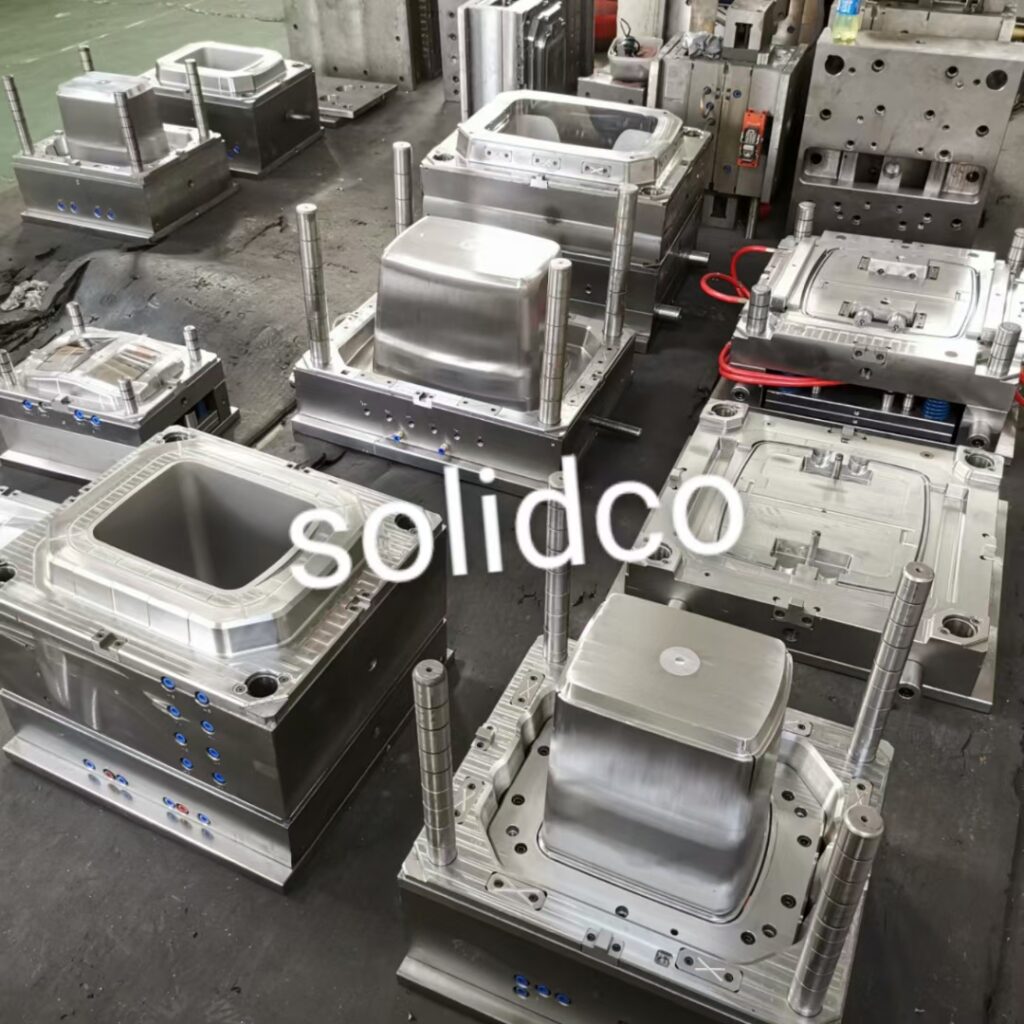