01 The meaning of draft angle Structural design of plastic parts: draft angle
Draft angle, as you can tell from the literal meaning, is the angle designed for the mold. To be precise, it is the mold ejection angle of the surface of the molding part in the direction parallel to the mold ejection direction, also called the draft angle.
02 Who designs the draft angle?
Since the draft angle is ultimately reflected in the mold, there will be a debate between designers of the draft angle, that is, whether the draft angle should be designed by the structural engineer or the mold engineer. There are currently two mainstream approaches to this point. :https://solidcomould.com/product-category/injection-mould/office-furniture-mould/
- Structural engineers need to complete drafting of all surfaces during the part design stage (except for individual structures that cannot be determined and require evaluation by mold engineers).
- The structural engineer is only responsible for drafting the appearance surface and key assembly surfaces. Other unimportant surfaces are left to the mold design stage for the mold engineer to draft based on experience.
Both approaches have their own advantages and disadvantages, and you should make a choice based on your specific circumstances:
For the first type,
advantage:
1) It can ensure that there is no interference in the structure, and that design requirements such as assembly gaps and dimensional deviations will not change, ensuring the quality of parts;
2) Save time for mold DFM review and communication, and avoid subsequent disputes over quality issues.
shortcoming:
1) Structural engineers are required to have extensive mold-related experience, otherwise the designed draft angle may not necessarily result in smooth mold release;
2) Since all surfaces require drafting, the workload of the structural engineer increases, and the project may be delayed if the project time is tight;
3) After drafting, the original vertical surface becomes an inclined surface, which causes inconvenience to subsequent structural modifications;
4) After drafting, more interference lines will be displayed on the engineering drawings, making it easy to mark errors.
For the second type,https://doi.org/10.1016/j.wear.2023.205000
advantage:
1) It saves the design time of structural engineers. Designed by experienced mold engineers, there will generally be no problems with mold release;
2) For structural engineers, subsequent structural modifications and engineering drawing annotations will be more convenient.
shortcoming:
1) Mold engineers may not necessarily understand the function of the product. They only think from the perspective of mold release and may not necessarily meet structural requirements, such as interference, clearance, size, strength, etc.;
2) The workload of mold engineers will increase. They usually remove the fillet before drafting, and finally fillet it back. After this step, the newly filled fillet may deviate from the previous fillet.
03 Types of draft angle
The draft angle is divided into the draft angle of the front mold surface and the draft angle of the rear mold surface. They are mainly distinguished by the parting surface. The parting surface divides the mold core into the front mold and the rear mold. The front mold and The draft angle that needs to be designed for the surface parallel to the mold ejection direction is called the draft angle of the front mold surface, and the opposite is called the draft angle of the rear mold surface. In addition, if the mold has side core pulling (inclined top and slider), Correspondingly, they are called the draft angle of the inclined top surface and the draft angle of the slider surface. The draft direction is based on the direction of the slider movement.
The drafting direction is generally based on the parting surface to ensure that the larger end after drafting is close to the parting surface, otherwise the demoulding cannot be smooth.
04 Why is it necessary to design the draft angle?
Draft angle is a process structure. If it is not required for modeling, theoretically there is no need to design draft angle for the product structure. However, due to the limitations of the molding process, such as injection molding, plastic products need to be taken out of the mold after cooling. , if the draft angle is not designed, the plastic parts will be difficult to remove from the mold. Recall that you must have encountered a situation where it is difficult to separate plastic stools that are stacked together. They are stools with a designed slope, not to mention that plastic parts without a designed draft slope need to be taken out from the mold.
- Why is it difficult to remove plastic parts from the mold without designing the draft angle?
In injection molding, molten resin flows into a closed mold and fills the cavity formed between the front and rear molds. Since thermoplastics shrink when cooled, the plastic has a tendency to shrink toward the mold core, and the shrunk plastic parts will become tight. Tightly adsorbed on the core of the mold. In addition to this, some of the plastic may pull away from the mold cavity walls (at a microscopic level), but most will still be in contact with the cavity walls.
During the mold opening process, whether the outer surface of the plastic part is in contact with the cavity wall or the inner surface of the plastic part is in contact with the core, the plastic part will experience frictional resistance (static friction) opposite to the direction in which the plastic part leaves the mold. From the friction force formula: f=μ×Fn, it can be seen that the size of the friction force is related to the roughness (μ) and shrinkage stress (Fn) of the contact surface; the shrinkage stress (Fn) is related to the draft angle.
After designing the draft angle, f=μ×Fn×cosα, the friction force f in the mold ejection direction decreases with the increase of the draft angle α. Generally, the draft angle is not very large. Obviously there is a limit to reducing static friction by draft angle.
The main function of the draft angle is that once the plastic part is detached from the mold, it will separate and no longer come into contact with the mold, and the friction will be eliminated; without designing the draft angle, the plastic part will turn to sliding friction after being detached from the mold. At the same time, for high-gloss appearance surfaces, a vacuum may form in the front mold cavity. The vacuum suction force will make it difficult for the plastic part to be completely separated from the front mold. The worst result is that the front mold is stuck to the front mold, and part of the structure of the rear mold of the plastic part is stretched and deformed.
- Benefits of draft angle:
Many times, draft can create a conflict of interest. For injection molding manufacturers, their focus is on molding and they hope to have a larger draft angle; for mold processing manufacturers, they find that processing angles on all cavities and core surfaces is a difficult task, and the originally simple features It only requires simple processing equipment and lower processing costs. After drafting, CNC or even EDM is required; for product designers, the draft angle may complicate the part design, and the appearance shape will also be affected by the draft slope. changed.
Regardless of the party, however, it is vital that we ensure that the molded parts meet the required quality standards. Without draft, you increase the chance of injection molding problems. This may unnecessarily increase production costs and delivery times. In addition to facilitating the removal of parts from the mold mentioned above, draft angle also has the following benefits:
Reduce the possibility of damaging the surface of the part due to friction during ejection;
Ensure uniformity and integrity of other surface textures and finishes;
Minimize the deformation of parts caused by uneven ejection;
Reduce the wear of molded parts and reduce the chance of damaging the mold;
Reduce overall cool down time by eliminating or reducing the need for complex ejection setups;
Direct and indirect reduction of overall production costs.
05 Principles of draft angle design
Ensure mold release requirements
Ensure structural function
Ensure appearance requirements
- Guarantee mold release requirements
- After the mold is opened, the plastic parts need to be left on one side of the rear mold to facilitate final ejection.
Taking the plastic parts out of the mold requires two steps:
1) First, the outer surface of the plastic part is separated from the front mold cavity wall. In this step, the mold generally does not have additional auxiliary separation structures, so the friction between the outer surface of the plastic part and the cavity wall is as small as possible.
2) Then, the inner surface of the plastic part is separated from the core wall of the rear model. In this step, the mold generally uses an auxiliary ejection structure such as an ejection pin, an inclined top or a push plate. The friction between the inner surface of the plastic part and the core is to a certain extent It should be greater than the friction between the outer surface of the plastic part and the cavity wall to ensure that the plastic part remains on the rear mold side during the mold opening process.
It can be seen from the above that since plastic has a tendency to shrink towards the core of the mold (that is, the shrinkage stress is large), when the roughness and draft angle are constant, the friction between the inner surface of the plastic part and the core will be greater than the outer surface of the plastic part. The friction with the cavity wall is large. At the same time, the ejection mechanism of the mold is usually on the rear mold side. Therefore, under normal circumstances, the core is designed on the rear mold and the cavity is designed on the front mold, that is, the plastic parts are The complex side is designed on the rear mold, and the relatively simple side (appearance side) is designed on the front mold.
But there are exceptions. For example, the inner surface of some parts is the exterior surface and no ejector pin marks are allowed. Then the core will be designed in the front mold and the cavity will be designed in the rear mold. In order to prevent sticking to the front mold, the front mold needs to be designed with an ejection assist. organization, as shown below.
There are also some parts that look almost the same from top to bottom and have no obvious appearance. For example, for the part in the picture below, it is not possible to quickly determine the front and rear molds of the part. For this type of parts, if there are no requirements, the front and rear molds can be on either side. In order to prevent the front mold from sticking. When designing the mold, as long as the draft angle of the rear mold is as small as possible and the draft angle of the front mold is as large as possible (within the tolerance range of the part size), the parts can stay in the moving mold after the mold is opened. This eliminates the need to design an ejection auxiliary mechanism in the front mold.
For the following structure with room for adjustment, the core glue position is changed from the original half of the front and rear molds to 1/3 of the front mold and 2/3 of the rear mold, which can reduce the risk of sticking to the front mold.
- Design of draft angle
There is currently no unified standard for the value range of the draft angle. Theoretical calculations are very difficult because it is difficult to establish a mathematical model of friction. Different injection molding parameters will also affect the final result. It may be obtained through simulation calculations. Some reference values, but they are time-consuming and labor-intensive. Generally, mold factories do not have the strength and time to do it. They are more based on experience. As a structural engineer, you need to understand this knowledge in order to target certain key points during the structural design stage. The structure takes the draft angle into consideration, reducing the number of subsequent modifications by the mold engineer and avoiding unnecessary trouble.
Determinants of draft angle:
1) Characteristics of molding materials
(Hard plastics have a larger draft angle than soft plastics, and soft plastics can even be forced to come off due to undercuts)
2) Shrinkage rate
(Because plastics with a large shrinkage rate have a greater tightening force on the core, plastics with a large shrinkage rate should have a larger draft angle than plastics with a small shrinkage rate)
3) Friction coefficient (
For some materials with low friction coefficient, such as PA and POM, the draft angle can be smaller than that of other ordinary plastics. The larger the friction coefficient of the product surface, the greater the draft angle. For example, the sun-textured surface requires a larger draft angle. )
4) Wall thickness
(As the wall thickness increases, the plastic wraps the core harder, and the draft angle should also be larger.)
5) Geometry
(Plastic parts with more complex shapes or more molding holes should have a larger draft angle, otherwise more ejection pins need to be arranged, and the ejection pin arrangement needs to be symmetrical and even to prevent uneven ejection force from causing warping and deformation of the part)
6) Transparent parts
(Parts with optical requirements must have a larger draft angle)
The specific value range of draft angle:
The geometric relationship between draft angle and draft surface height: tanθ=X/H;
Among them, θ = draft slope; H = draft surface height; X = reduced wall thickness (or tilt deviation).
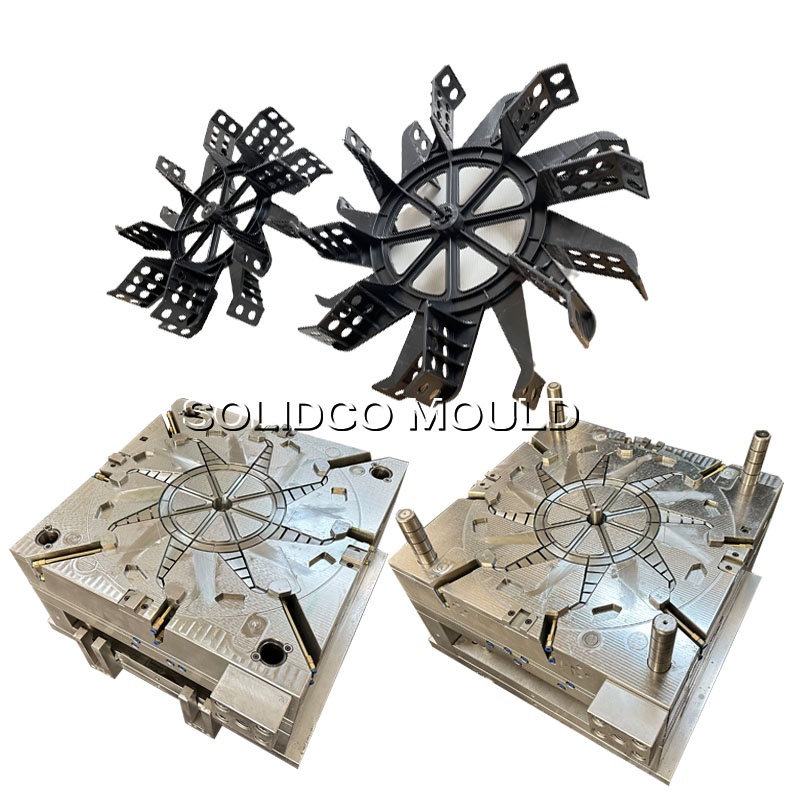