- Two-color injection molding is realized on a two-color injection molding machine. One material is injected into a product, and then the mold is flipped on the two-color machine to jump to the mold cavity corresponding to another injection plastic barrel. This part is used as an insert. Another material is injected on top to form an integrated dual-material product. The injection molding machine has dual barrels and dual mold cavities. The injection molding process is to produce products of two materials at the same time, but the products in one cavity will be used as inserts to enter the next cavity.
The essential difference between two-color injection molding and in-mold injection molding - The other is two-step injection molding (in-mold injection molding). A component of one material is molded on an injection molding machine. The component is placed as an insert in another mold, and then the second material is injected.
The simplest explanation is that. Two-color injection molding is a one-shot molding process using an injection molding machine, while in-mold injection molding is a single or multiple molding process for included products.
Let’s give a simpler explanation:
Two-color injection molding involves throwing the material into the injection molding machine, and the finished product you need comes out.
In-mold injection molding requires that the products to be combined are put in before molding, and then integrated into one through injection molding.
For specific samples, you can see the methods of toothbrush handle (two-color injection molding) and mobile phone data cable (in-mold injection molding)
【two】
How to choose between two-color injection molding and in-mold injection molding
https://doi.org/10.1016/j.jmapro.2024.02.021
- What kind of products require two-color injection molding?
A. Products with high appearance requirements
The appearance material is hard glue and transparent, and no obvious impurities can be seen in the appearance of the transparent parts, and the texture looks thick.
For example: Apple wireless mouse, LeTV power bank. As shown below:
B. Products with multi-colored appearance and no surface treatment
The appearance material is hard glue in multiple colors and does not undergo surface treatment. Most of them are used in light-transmitting products.
For example: keyboard buttons, mouse, mobile phone protective case, etc. As shown below:
C, products with strong structural integration
The appearance material is soft glue and needs to be used frequently. The glue cannot be opened or loosened during use. It is a product with high performance requirements and high bonding requirements.
For example: toothbrush handles, tool products screwdrivers, three-proof products mobile phones and watches, etc. As shown below:
So what points need to be paid attention to when designing the structure?
a. Since the appearance is a transparent part, the wall thickness must be uniform during structural design, and there must be no unevenness, unless it is deliberately designed to have such a texture.
b. When used as a transparent light guide, it still needs to be designed as uniformly as possible, with less uneven glue positions and less reinforcement ribs to prevent light from passing through and seeing the shadow of the internal structure.
c. When the first layer is made of hard glue, the thinnest part of the structural surface wall thickness should not be less than 0.6mm to prevent the injection molding from not being full of glue.
d. When the appearance surface of the second layer is made of hard glue, the wall thickness is designed to be between 0.6-2.0mm, and the conventional design is 0.8mm to prevent appearance problems caused by molding defects.
e. When the appearance surface of the second layer is made of soft rubber, the wall thickness is designed to be between 0.4-2.0mm, and the conventional design is 0.8mm to prevent appearance problems caused by molding defects.
g. When the second layer of exterior surface is made of soft glue, try not to disconnect it during design. Try to design it so that one glue entry point can cover all the exterior design surfaces.
https://solidcomould.com/product-category/injection-mould/household-mould/
- What kind of products require in-mold injection molding?
A. Products with built-in electronic components
The exterior material is hard glue or soft glue, and the interior is wrapped with electronic materials, such as PCB boards, flexible FPC boards, or electronic devices, etc.
For example: wires, electronic components, etc. As shown below
B. Products with metal materials inside
The exterior material is hard glue or soft glue, and the interior is wrapped with metal materials, which mainly play the role of overall reinforcement or electronic structure linking.
For example: the front case of mobile phones, smart watch straps, utility knives, etc. As shown below
C, products combining multiple plastic materials
The exterior material is hard rubber or soft rubber, and the interior is wrapped with hard plastic material. This is mainly to save the unit price and provide the effect of multi-color injection molding.
For example: rugged mobile phone casing, solid plastic bracket, etc. As shown below
So what points need to be paid attention to when designing the structure?
a. When there are electronic components inside, you need to consider the melting point of the component that can withstand high temperatures. If it is lower than the melting point of the wrapping plastic, in-mold injection molding cannot be achieved.
b. In-mold injection molded products need positioning points when placed into the mold to prevent the products in the package from being deformed due to high pressure during injection. (Look carefully at the USB data cable plug, there will be two small holes of about 0.6m to limit the internal components)
c. When the first layer is made of solid hard plastic, you need to consider whether the product you design meets the production capacity requirements, because solid plastic is much slower to mold, which is 1/5 to 2/5 of the speed of ordinary products.
d. When the first layer is made of metal, you need to consider the bonding and peelability of the metal and plastic. Usually you need to design a dovetail undercut or a round hole to fix and pull the plastic to prevent it from coming off.
e. When the appearance surface of the second layer is made of hard glue, the wall thickness is designed to be between 0.6-2.0mm, and the conventional design is 0.8mm to prevent appearance problems caused by molding defects.
g. When the second layer’s appearance surface is made of soft rubber, the wall thickness is designed to be between 0.4-2.0mm, and the conventional design is 0.8mm to prevent appearance problems caused by molding defects.
h. When the second layer of plastic is made of soft plastic, the peeling test needs to be considered during design. Then when designing the first layer of plastic, you need to design a lot of clamping positions to fill them in when the second layer of soft plastic is formed. You can Plays a pulling role to prevent the peel test from failing.
【three】
The advantages and disadvantages of two-color injection molding and in-mold injection molding
- What are the advantages of two-color injection molding?
A. Two-color injection molding products have high bonding and strong adhesion. To put it simply, the hard plastic is still hot when it is injected in the first step, and immediately enters the second cavity of the injection molding machine. It does not absorb moisture during the intermediate transfer process, and is easily ablated by the high-temperature soft plastic melt on the surface. The ultra-thin layer has no effect of water vapor being adsorbed on the surface.
B. Two-color injection molding products have beautiful appearance, simple process, high product precision, stable quality, and one-piece molding in place to reduce secondary pollution caused by transfer to the environment and other poor appearance.
- What are the disadvantages of two-color injection molding?
A. The mold cost is high and 2 sets of front molds are required.
B. The unit price of the product is high. Once one shot is defective, the entire product will be scrapped, which will increase the unit price of the product.
- What are the advantages of in-mold injection molding?
A. The products have strong commonality, high inclusiveness, wide range of uses, and the unit price of molds is low.
B. It has high plasticity and diversity and can hide the electronic part more closely.
C. It is wrapped with plastic or hardware. The overall structure has strong rigidity and high impact resistance.
- What are the disadvantages of in-mold injection molding?
A. The structural accuracy is unstable, the overall flatness of the product is poor, and the defective rate is high.
B. Since the shrinkage rates of the inner metal and outer plastic products are inconsistent, it is easy to cause uneven shrinkage of the exterior surface.
C. Review of the molding process, resulting in long overall molding time and average production capacity.
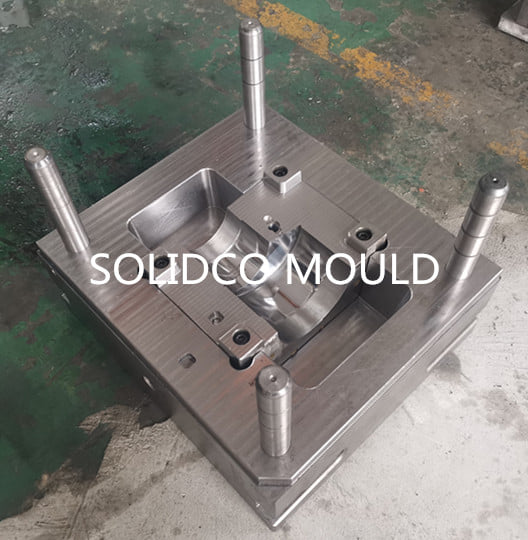