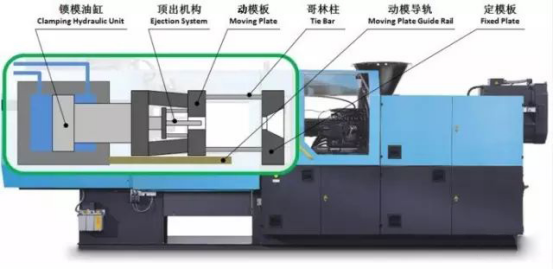
Start mold closing clamping
1.Starting mold clamping pressure: The initial setting value is 25. When the pressure is too low and the speed is too slow, you can try to increase the speed. If the pressure is too low and the speed cannot be increased to the required level, try adding +5 each time.
Note that when the pressure is set to a large value, the moving template will be instantly high-pressured to change the static state to motion, which will cause huge friction between the moving template hole and the tie rod.
Over time, the wear of the machine’s moving template hole and the tie rod will be accelerated, affecting the stability and precision of the moving template movement, which may affect the production of individual molds with high precision requirements for the clamping mechanism.
2.Starting mold clamping speed: It depends on the actual situation, but be careful not to move too fast. The speed should be a continuous movement with the next clamping action, rather than an obvious pause in the action switch.
It is best to set the speed high and the pressure low, and control the speed by pressure.
Low pressure clamping
Push the mold at low pressure and low speed, starting from the distance that needs safety protection until the mold is completely closed.
1. Low-pressure mold closing speed: It depends on the actual situation. The speed should be slow.
If the speed is too fast, even if the low pressure is set, the inertial motion still has a huge impact destructive force. Slide position deviation, ejector breakage…
When unexpected hard obstacles appear, the mold closing action is entered. Under the effective low-pressure and slow mold closing protection parameter conditions, the impact damage is greatly reduced. In fact, this speed can be several tens, and then it can be left unchanged.
Then the pressure can be adjusted very low, such as 5, for testing. The speed can be controlled by pressure, and then the pressure can be increased step by step to the appropriate mold closing protection speed.
2.Low-pressure mold closing pressure: You can first adjust the speed very high and the pressure very low, such as 5, for mold closing test. Because the pressure is low, even if the speed is set very high, the mold closing speed will not be very fast without the support of pressure.
The speed can be controlled by pressure. On the basis of 5, it can be increased little by little to the ideal mold closing protection speed, and the mold can be closed at the lowest pressure.
3. Low-pressure mold closing starting position: (i.e. the end position of the previous mold closing) This should be set according to the size and structure of the mold.
The value is generally between 5-20 cm before the mold is closed. This position is up to you. Many people set the mold too close and start using low pressure.
The distance of low-pressure protection should be obtained in advance. When the mold is impacted by the previous high pressure speed, the slide position is offset, the ejector pin is broken, etc.,
there are unexpected hard obstacles, and the low-pressure protection is invalid at this time. It is too late (key point), etc.
4. Low-pressure mold closing end position (i.e. high-pressure mold clamping start position): This parameter is the position where the mold is just completely closed, that is, the moving mold plate has stopped at the end.
When debugging, first adjust the low-pressure pressure and speed, then set the position to 0, and close the door to manually close the mold to test and get a low-pressure mold closing position value;
For example, this value is 2.2. The size of this value is affected by the electronic ruler setting adjustment, mold adjustment tightness, mold clamping pressure, and this value is affected by machine accuracy and small debris on the mold surface.
There may be slight changes each time the mold is closed, so the end position should be set a little larger, such as adding 0.2 to 2.4 (reference plus 0.1-0.3), with the lowest position, to accurately protect the mold.
If the position value obtained by the low-pressure mold closing test is not set a little larger, and 2.2 is used directly, the low-pressure mold closing position may often be greater than 2.2, and the low-pressure position cannot be ended and cannot be switched to high-pressure mold clamping.
However, more people set the mold to be several centimeters or longer before it is completely closed, and then terminate the low pressure, and start using high pressure. The low pressure protection is invalid.
It is often seen that some molds are accidentally closed with the formed products that have been ejected, and the steel cavity is deformed by pressure.
High pressure clamping
1. High pressure clamping pressure: The initial setting value is 60. When it cannot be met, increase the pressure by +10 each time. If the pressure is too high, it is unnecessary to increase the machine load…
2.High pressure clamping speed: The initial setting value is 25. When it cannot meet the needs, try to increase the pressure first. If it doesn’t work, try to increase the speed by +10 each time.
You should not hear too loud noise when high pressure clamping. If the speed is doubled, the friction loss of the clamping mechanism will increase by N times.
Contact Person: Alex Chu
WhatsApp/ WeChat: 0086 18968677763
Email: sc10@solidcomould.com
Website: www.solidcomould.com