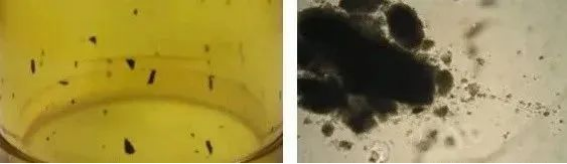
Black spots and impurities are important factors that cause scrap rates in normal production processes. They mainly affect the appearance of products and lead to product scrapping.
Impurities and most black spots are foreign substances and have nothing to do with the raw materials themselves, while a small number of impurities and black spots are caused by the raw materials themselves.
Classification
Impurities and black spots before molding
- During the processing of raw materials, due to various reasons, foreign matter is mixed in, resulting in black spots on the raw materials.
- Black spots are caused by impure granulation.
- Raw materials mixed with masterbatch or spotted crushed pieces and scraps
- Impurity of materials, high melting point materials are mixed into low melting point materials.
- Impurities may be mixed in during packaging, transportation and storage. The obvious feature is that after the raw materials are unpacked, careful observation shows that foreign matter and impurities can be seen on the surface of the granular materials.
- Impurities and foreign matter during the feeding process.
- Carbonization of raw materials, this kind of black spots are generally larger in size, and the appearance diameter of large black spots can reach 1~2mm, and most black spots are thicker.
Raw materials accumulate for a long time or are partially exposed to high temperature, decompose, coke, and carbonize into blocks. The flow is sheared and broken at the screw or nozzle, etc.
Causes of raw material carbonization:
If the melt temperature is too high, the material temperature will cause overheating and decomposition, forming carbides, especially for some heat-sensitive materials with a narrow temperature range, and the temperature at the end of the barrel must be controlled not to be too high.
Carbonization of material accumulation. If the molten plastic stays in a certain place for too long, carbonization and accumulation will occur, causing black spots.
The areas that may cause material retention include the connection between the nozzle and the barrel, the barrel wall, the melt ring, the contact between the nozzle and the gate, the hot runner bend, and the dead corner of the main runner.
If the gap between the barrel is too large, the gap between the barrel and the screw is too large, which will cause the material to be retained in the barrel, and the retained material will decompose after long-term overheating, resulting in black spots.
Degradation and discoloration of additives. Additives include antistatic agents, ultraviolet and infrared absorbers, and general dyes. Their properties are generally more active than raw materials.
Under the shear force of processing temperature, when the raw materials are not decomposed, the additives have already decomposed and become dark, yellow-brown or even black, forming black spots and impurities during molding.
Black spots and impurities caused by external factors during production
- The mold material is not good, and iron powder will fall off the parting surface, molding surface or penetration surface, causing black spots.
- The ejector is rough and easy to burn, and iron powder will fall off, causing black spots.
- The slider grinds iron powder, causing black spots.
- The slider leaks water and rusts or other stains. The rust and stains are thrown out by the slider and fall on the product to form black spots.
Identification of black spots
- If black spots appear on the entire surface of the product, and there are black spots deep in the product, they should be black spots before molding.
- If black spots only appear on the surface, they should be black spots during molding.
- If they are only distributed in specific areas of the surface at the same time, they are undoubtedly black spots during molding.
- If the black spots are large, they should be carbonized black spots of the raw material.
- If the black spots are dark, brittle, loose and porous, they can be determined as carbonized black spots.
- If the density of black spots is particularly large, check the raw materials for obvious impurities. Generally, it should be a phenomenon that the original material has not been cleaned up just after the material is replaced. Otherwise, the cause of the material should be checked.
Contact Person: Alex Chu
WhatsApp/ WeChat: 0086 18968677763
Email: sc10@solidcomould.com
Website: www.solidcomould.com