Plastic product structure design Key points of plastic product structure design
- Glue thickness (glue position):
The glue thickness (overall shell) of plastic products is usually around 0.80-3.00. If it is too thick, it will easily shrink and produce bubbles. If it is too thin, it will be difficult to fill the glue. For large products, the glue thickness should be thicker, for small products, thinner. For general products, the glue thickness should be thicker. Take 1.0-2.0 as more. Moreover, the glue position should be as uniform as possible. If necessary, the local area can be appropriately thicker or thinner, but it needs to be gradual and not sudden. The principle is to not shrink and to be able to fill the glue. Generally, the plastic glue thickness is less than 0.3 It is difficult to run the glue when the thickness is 0.2-0.3, but soft rubber and rubber can also run full of glue when the glue thickness is 0.2-0.3. - Strengthen tendons (bone position):
Most plastic products have reinforcing ribs, because the reinforcing ribs can greatly increase the overall strength of the product without increasing the overall rubber thickness. It is especially useful for large and stressed products, and can also prevent product deformation. The thickness of the reinforcing rib is usually 0.5-0.7 times the overall rubber thickness. If it is greater than 0.7 times, it will easily shrink. When the height of the reinforcing rib is large, a slope of 0.5-1 is required (due to the large mold release resistance). When the height is short, the slope is not necessary. - Draft angle:
All plastic products must have a draft angle, except for those with a shallow height (such as a flat plate) and those with special requirements (but when the side wall is large and there is no draft angle, it needs to be aligned). The mold ejection angle is usually 1-5 degrees, usually about 2 degrees, which depends on the size, height, and shape of the product. The principle is to ensure smooth demoulding and not affect the use function. The slope of the front mold of the product is usually 0.5 degrees greater than the slope of the rear mold, so that the product can stay in the rear mold when the mold is opened. Generally, slopes are required for pillow positions, insertions, and penetrations, and the upper and lower differences (that is, the difference between the size of the big end and the size of the small end) should be greater than 0.1 on one side. - Rounded corners (R corners):
In addition to special requirements for plastic products that specify sharp edges, the edges are usually rounded to reduce stress concentration, facilitate the flow of plastic, and facilitate demolding. The minimum R is usually greater than 0.3, because it is difficult to achieve on molds with an R that is too small. - hole:
From the perspective of facilitating mold processing, it is best to make the hole a round hole with a regular and simple shape. Try not to make a complex special-shaped hole. The hole diameter should not be too small. The ratio of hole depth to hole diameter should not be too large. Thin and long holes should not be made. The mold core is easy to break and deform. The distance between the hole and the outer edge of the product should be greater than 1.5 times the hole diameter, and the distance between holes should be greater than 2 times the hole diameter, so that the product has the necessary strength.
Holes that are parallel to the opening direction of the mold are usually formed with a core (can be inlaid or extended) or by punching or inserting. Holes that are not parallel to the opening direction of the mold are usually made with rows or inclined tops. , on the premise of not affecting the use and assembly of the product, the holes in the side walls of the product should be made into holes that can be punched and inserted into the molding when possible.
6. Boss (BOSS):
Bosses are usually used for the shaft-hole fit of two plastic products, or for the assembly of self-tapping screws. When the BOSS is not very high and the mold is ejected with a cylinder, there is no need to make a slope. When the BOSS is very high, cross ribs (ribs) are usually added to the outside. The cross ribs usually have a slope of 1-2 degrees. The BOSS also needs to be sloped depending on the situation. When the BOSS and the pillar (or another BOSS) are matched, the matching clearance is usually an assembly clearance of 0.05-0.10 on one side in order to adapt to the position error generated during the processing of each BOSS.
When BOSS is used to assemble self-tapping screws, its inner hole should be 0.1-0.2 smaller than the thread diameter of the self-tapping screws on one side so that the screws can be locked. For example, when assembling with M3.0 self-tapping screws, the inner hole of BOSS is usually Ф2.60-2.80.
- Inserts:
When an existing metal or plastic part is placed in the mold and re-molded, the existing part is called an insert. When a plastic product is designed with an insert, it must be considered that the insert must be positioned completely, accurately, and reliably in the mold. It must also be considered that the insert must be firmly connected to the molded part. When the rubber coating is too thin, it will not be easy to be firm. Also consider not leaking glue. - Product surface texture:
The surface of plastic products can be smooth (the mold surface is light-saving), sparkle pattern (the mold cavity is formed by electrical discharge machining by copper workers), etched surface (sun-textured surface) and engraved surface with various patterns. When the depth of the grain surface is deep and the number is large, the demoulding resistance will be large, and the demoulding slope must be increased accordingly. - Word:
The characters on the surface of plastic products can be embossed or concave. It is easy to make corresponding concave cavities for convex characters on the mold, but it is more difficult to make convex centers for concave characters on the mold. - Thread:
The threads on plastic parts are usually not very precise, and a special thread removal mechanism is required. For those with low precision requirements, the structure can be simplified into a structure that can be forcibly demoulded.
11. Support surface:
Plastic products usually do not use the entire surface as a supporting surface, but use separate bosses, bumps, and ribs for support. Because it is difficult for plastic products to cover a large absolute plane, they are prone to deformation and warping.
- Assembly form of plastic products:
- The ultrasonic line joining assembly method is characterized by being easy to do on the mold, but requires a special ultrasonic machine during the assembly process, which increases the cost and cannot be disassembled.
The cross-section of the ultrasonic line is usually made into a triangle with a width of 0.30 and a height of 0.3, with 2mm intervals of 5-10mm in the length direction;
- The self-tapping screw assembly method is characterized by being easy to do on the mold, but it increases the assembly process, increases the cost, and is troublesome to disassemble;https://doi.org/10.1016/j.matpr.2022.10.039
- The hook-button assembly method is characterized by complex mold processing, but easy assembly, and can be repeatedly disassembled and used multiple times. There are many forms of hooks. It is necessary to avoid the local glue level at the hook being too thick, and it is also necessary to consider the convenience of mold making at the hook. The hooks should be appropriately tight and easy to assemble and disassemble. The mating surfaces should be close to each other and leave appropriate gaps on other surfaces.
- The BOSS shaft-hole assembly method is characterized by easy mold processing, easy assembly, and easy disassembly, but its disadvantage is that the assembly is not very firm.
- Tooth mouth:
The mating contact surface of two plastic products is usually made with a tooth mouth. The depth of the tooth mouth is usually about 0.8-2.5, leaving a gap of about 0.1 on the side. When the depth is deep, the slope is 1-5 degrees, and the depth is often 2 degrees. When it is shallow, there is no need to make a slope. The upper and lower mating surfaces of the tooth mouth are usually close to each other (i.e. 0 gap). https://solidcomould.com/product/car-bumper-mould-plastic-1/
- Beautiful line:
An aesthetic line is usually made on the mating surface of two plastic products. The width of the aesthetic line is usually 0.2-1.0, depending on the overall size of the product.
15. Surface treatment methods of plastic products:
Commonly used methods include oil spraying, silk screen printing, hot stamping, printing, electroplating, engraving, etching, polishing, coloring, etc.
16. Commonly used metal materials include:
Stainless steel, copper alloy (brass, bronze, phosphor bronze, red copper), spring steel, spring, aluminum alloy, zinc alloy.
- Commonly used anti-rust methods for metal materials: electroplating, applying anti-rust oil, and spraying anti-rust paint.
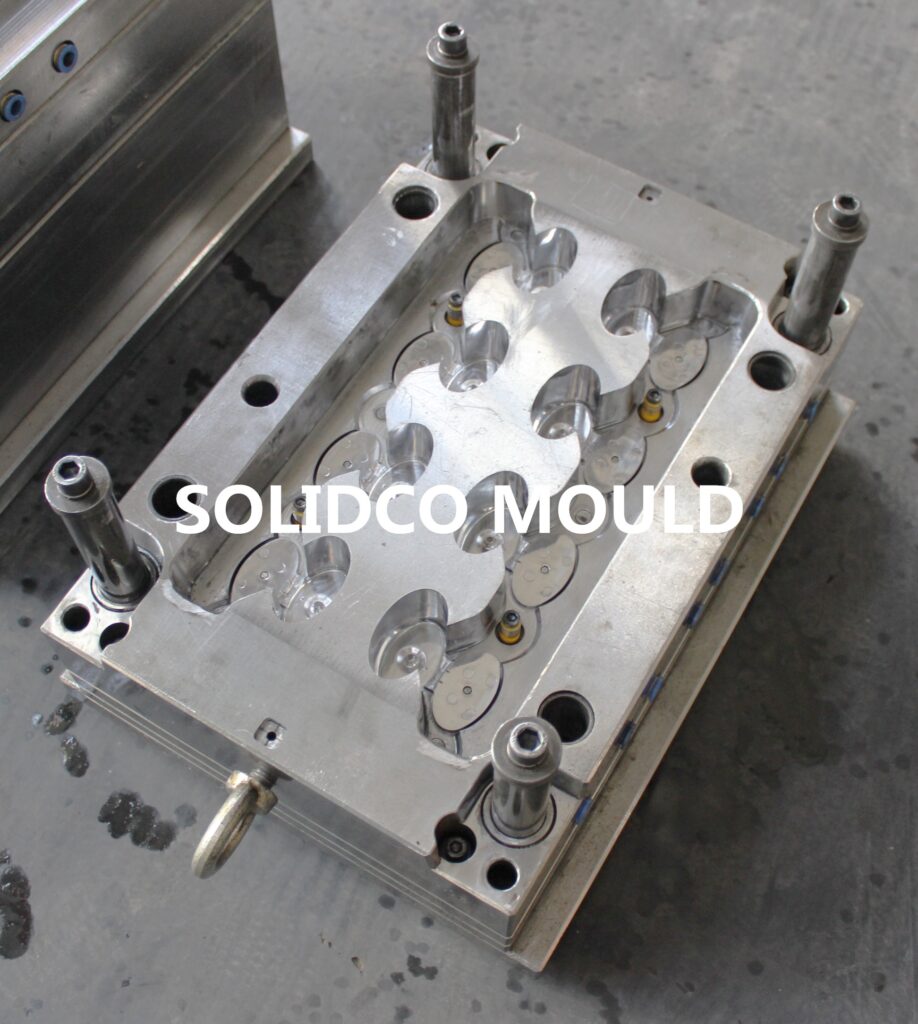